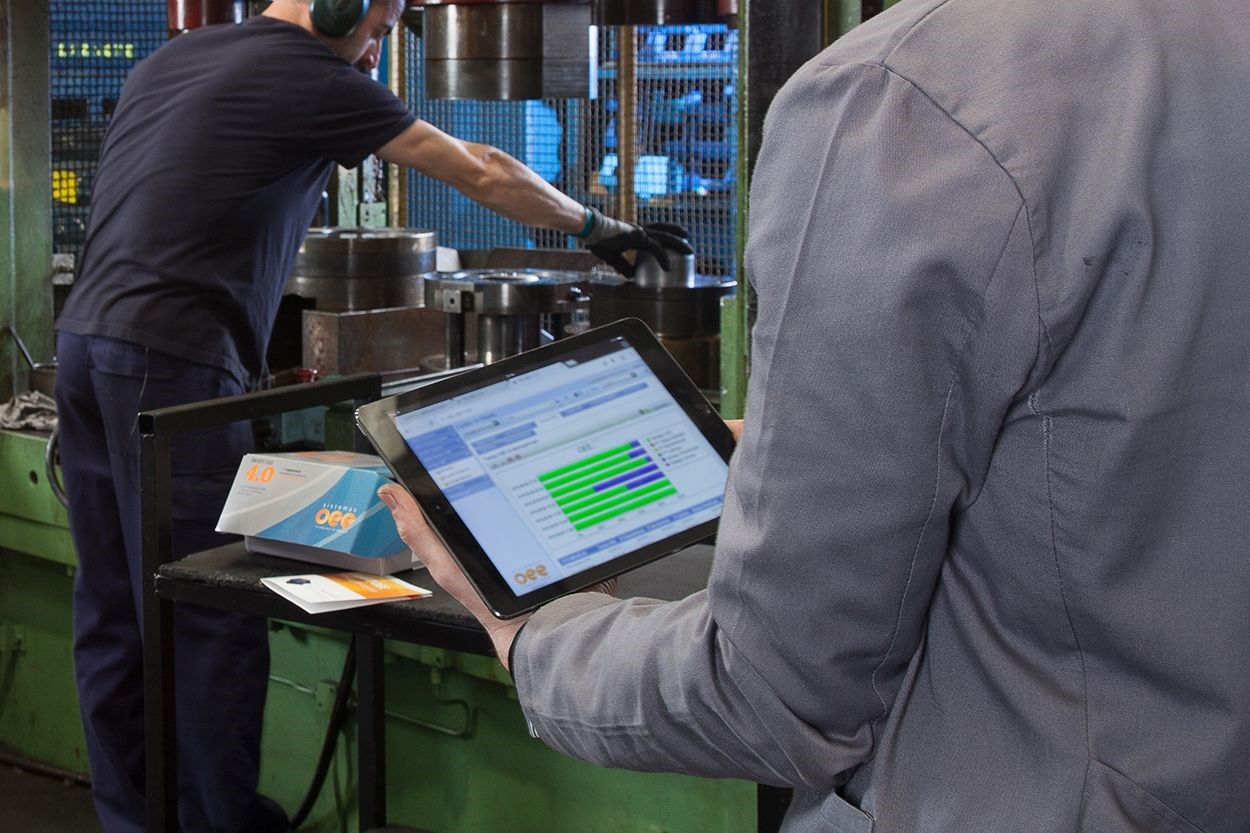
OEE (efictividad global del equipo) es el estándar de oro para medir la productividad de fabricación. En pocas palabras: identifica el porcentaje de tiempo de fabricación que es realmente productivo. Una puntuación OEE del 100% significa que está fabricando solo piezas buenas, lo más rápido posible, sin tiempo de parada.
En el lenguaje de OEE, eso significa 100% de calidad (solo piezas buenas), 100% de rendimiento (lo más rápido posible) y 100% de disponibilidad (sin tiempo de parada).
La medición de OEE es una de las mejores prácticas de fabricación. Al medir la OEE y las pérdidas subyacentes, obtendrá información importante sobre cómo mejorar sistemáticamente su proceso de fabricación. OEE es la mejor métrica para identificar pérdidas, evaluar el progreso y mejorar la productividad de los equipos de fabricación (es decir, eliminar el desperdicio).
TIEMPO PLANIFICADO DE PRODUCCION
Del tiempo total disponible en el día, mes y año se resta la pérdida programada, que incluye todo el tiempo que debe excluirse del análisis OEE porque no hay intención de ejecutar la producción durante este tiempo (por ejemplo, paradas de planta, descansos / almuerzos o períodos en los que no hay pedidos). La pérdida programada no es parte de OEE.
El tiempo restante es el tiempo de producción planificado. La OEE comienza con el Tiempo de producción planificado y examina todas las pérdidas de eficiencia y productividad que se producen dentro de ese tiempo, con el objetivo de reducir o eliminar estas pérdidas.
El tiempo de producción planificado es el tiempo que se espera que produzca el equipo de fabricación.
Existen tres factores OEE, cada uno de los cuales tiene en cuenta un tipo diferente de pérdida. Estos son: Disponibilidad, Desempeño y Calidad.
DISPONIBILIDAD
Este factor tiene en cuenta la pérdida de disponibilidad, que incluye cualquier evento que detenga la producción planificada durante un período de tiempo apreciable (generalmente varios minutos; el tiempo suficiente para que un operador registre un motivo).
Ejemplos de situaciones que crean pérdida de disponibilidad incluyen paradas no planificadas (como fallas de equipos y escasez de material) y paradas planificadas (como tiempo de cambio). El tiempo de cambio se incluye en el análisis OEE, ya que es un tiempo que de otro modo podría utilizarse para la fabricación. Si bien puede que no sea posible eliminar el tiempo de cambio, en la mayoría de los casos se puede reducir significativamente.
El tiempo restante después de restar la pérdida de disponibilidad se denomina tiempo de ejecución.
El tiempo de ejecución se calcula restando el tiempo de inactividad del tiempo de producción planificado
RENDIMIENTO
Este factor tiene en cuenta la pérdida de rendimiento, que representa cualquier cosa que haga que el proceso de fabricación se ejecute a una velocidad inferior a la máxima posible cuando se está ejecutando (incluidos los ciclos lentos y las paradas pequeñas).
Ejemplos de situaciones que crean pérdida de rendimiento incluyen desgaste de la máquina, materiales deficientes, alimentación errónea y atascos.
El tiempo restante después de restar la pérdida de rendimiento se denomina tiempo de ejecución neto.
El tiempo de ejecución neto es el tiempo que queda después de restar las pérdidas de rendimiento, programación y disponibilidad.
CALIDAD
Este factor tiene en cuenta la pérdida de calidad, que representa las piezas fabricadas que no cumplen con los estándares de calidad previstos.
Un ejemplo de cosas que crean pérdida de calidad incluyen desechos y piezas que necesitan retrabajo. La calidad OEE es similar a First Pass Yield, ya que define las piezas buenas como piezas que pasan con éxito por el proceso de fabricación la primera vez sin necesidad de volver a trabajar.
El tiempo restante después de restar la pérdida de calidad se denomina tiempo de productividad total.
El tiempo completamente productivo es tiempo productivo después de restar todas las pérdidas
Nuestro objetivo no es simplemente medir la OEE, es maximizar el Tiempo Totalmente Productivo.
Como se puede ver, los conceptos centrales de OEE son bastante simples y los tres factores de OEE realmente ayudan a enfocarnos en las causas subyacentes de la pérdida de productividad.
Podemos profundizar aún más en las pérdidas de productividad al comprender las seis grandes pérdidas (tema que será materia de otro artículo).
También podemos ampliar el análisis de OEE un paso más si tenemos en cuenta un cuarto factor: la utilización. Esto nos lleva al ámbito de TEEP (materia de una tercera entrega).
Fuente: Extraido y traducido de la página web OEE.COM de Vorne.